Specific research and development
Ultra RS regularly participates in several R&D projects with the aim of developing control processes adapted to industrial needs. Here are some examples of projects in which we are involved:
Development and validation of a specific device for the control, by ultrasound, of the tightening of screws by hydraulic process.
ULTRA RS is working on the development of this technique by proposing a global solution of tightening incorporating both ultrasonic control and the hydraulic pump part. Using to a control loop, the tightening operation can be carried out at the desired value in a precise and reproducible manner.
Measurement of thermal stresses in the rails
The previous version of the thermal stress measurement device designed by the company Ultra RS in partnership with SNCF and called Skill 100 was used for track tests. This system has shown its effectiveness with consistent results for new rails but it has also shown heterogeneous results during other tests on old rails. The rail that has been the subject of all previous tests is a rail that has never been run. New rails have the advantage of having a regular profile and homogeneous mechanical characteristics. However, the rails undergo changes due to the passage of trains and the environment such as: work hardening, wear, impact of ballast …
The objective of this research project is to develop a measurement technique to overcome parameters that interfere with measurements in order to make the device for measuring thermal stresses on running rails more reliable.
In this perspective, a protocol bringing together a first series of tests was developed in order to highlight the disturbing phenomena of the measurement:
- nature of the coupling agent
- state of the surface (with and without oxidation)
- variability of the force applied to the device.
Residual stresses in the tubes
Development of a method for measuring residual stresses by ultrasound in tubes, used for automotive and aeronautical applications. This project is a cooperation between Ultra RS in France and a regional company. Ultra RS has developed a system to measure residual stresses in different materials. Our partner has significant expertise and experience in material related problems in tubes.
The main objective of this project is to develop and propose an industrial solution to be installed on a production line in order to verify the conformity of the tubes with respect to the values of the residual stresses induced by straightening operations.
NANOSURF (nanostructure)
The goal of the NANOSURF project is the study, development and fine-tuning on industrial parts of a Superficial Nanocrystallization process patented in 2000 by the University of Technology of Troyes. The principle of this process is based on the setting in motion of perfectly spherical balls by means of ultrasound. These balls strike the surface of the part to be treated in a random fashion, which generates on the surface of massive materials a crystalline nanostructure with grains of a size less than 20 nm and a thickness of a few tens to a hundred micrometers. It has been shown that this surface nanostructure gives parts exceptional mechanical and surface properties.
The project has two components:
-
A more fundamental study on the understanding of the generation of the nanostructure and its role in improving the macroscopic properties of the treated part. The goal of this step is to optimize the generated nanostructure.
-
An industrialisation study of the process: the design and development of portable equipment capable of processing parts of complex geometry and / or large size. The development of a non-destructive ultrasound technique will make it possible to control the quality of the nanostructures generated on industrial parts and can be directly integrated into production lines. This is where Ultra RS comes in.
EVAPREC
The objective of this project is the development of a non-destructive technique (using subsurface ultrasonic waves) for controlling the loading force present in prestressing bars both during their installation but also during time after they are put into service. Controlling the stresses in the prestressing bars still poses many problems:
- Ignorance of the real tension introduced into the bars during their assembly.
- The current impossibility of controlling the evolution of this tension over time in an already assembled structure.
Ultra RS
We develop solutions for non-destructive testing and material characterization by ultrasound. Industrialists of all kinds, to ensure the quality, reliability and safety of your production and assembly lines and to achieve significant savings, contact us!
Solutions
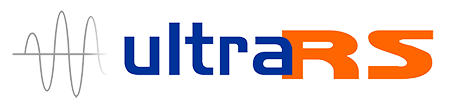
16 rue de la Prairie,
77700, BAILLY-ROMAINVILLIERS
+33 (0)1 83 38 94 72
ISO 9001 Certified